Arc Flash Hazard Analysis – Full Risk Assessment
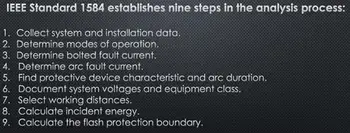
Arc Flash Hazard Analysis evaluates electrical hazards, calculates incident energy, defines PPE requirements, and ensures NFPA 70E compliance to protect workers and reduce injury risks in hazardous environments.
What is an Arc Flash Hazard Analysis?
Arc flash hazard analysis is a safety study used to identify potential arc flash events and their severity in electrical systems.
✅ Identifies arc flash boundaries and incident energy levels
✅ Determines proper PPE categories to protect electrical workers
✅ Ensures compliance with NFPA 70E and OSHA safety regulations
Request a Free Training Quotation
NFPA 70E and CSA Z462 Compliance in Hazard Analysis
"Partially energized" refers to a condition where certain parts of an electrical circuit or piece of equipment remain live or carry voltage, even when other parts have been shut off or isolated. This presents a hidden danger, as it can create a false sense of security for workers who may assume the entire system is safe to handle. Understanding and identifying partially energized systems is crucial for preventing electrical accidents and ensuring proper lockout/tagout procedures are followed. To grasp the implications of partially energized systems, it's essential to understand the basics of electrical safety. This includes recognizing potential hazards and implementing safety measures to prevent accidents. For a comprehensive overview, refer to the article on Electrical Safety.
Understanding Incident Energy and Its Role in Arc Flash Risk
To protect workers from electrical hazards, every facility must complete an arc flash hazard analysis that includes a thorough arc flash risk assessment. This process evaluates potential dangers from shock and arc flash incidents by analyzing system configurations, available fault currents, and the settings of protective devices. A critical outcome of this analysis is defining an accurate arc flash boundary, which represents the minimum working distance a qualified worker must maintain to avoid serious injury. These boundaries help guide the selection of personal protective equipment (PPE) and safe work practices, ensuring compliance with safety standards like NFPA 70E and CSA Z462.
PPE Categories: Choosing the Right Gear for Shock Protection
A proper analysis involves identifying all energized electrical equipment where exposure to electrical hazards may occur. By calculating incident energy levels and establishing boundary distances, safety professionals can determine the correct PPE category for each task and apply appropriate labels to the equipment. The goal is not only to meet regulatory requirements but also to develop an arc flash plan that proactively minimizes risk. Whether updating safety protocols, training personnel, or preparing for audits, a detailed hazard analysis forms the backbone of any effective electrical safety program, empowering teams to work confidently in high-risk environments.
Step-by-Step Arc Flash Risk Assessment and Labeling Requirements
This evaluates the likelihood and severity of arc flash events across an entire electrical system. It includes gathering detailed system data, identifying high-risk equipment, evaluating worker exposure, and developing a plan to control or eliminate hazards. The goal is not only to calculate energy levels but to translate those findings into practical safety measures — PPE selection, arc flash labeling, boundary setting, and training.
It plays a key role in a broader electrical safety audit, helping organizations identify areas for risk mitigation and improve overall worker protection. By conducting an NFPA 70E assessment, employers can ensure compliance while implementing practical steps for electrical incident prevention across their facilities.
Understanding the nuances of arc flash hazards can provide insights into the dangers of partially energized systems. The Arc Flash Questions article addresses common queries and offers detailed explanations on boundaries, PPE, and safety standards.
Arc Flash Hazard Analysis vs. Arc Flash Analysis
While the terms are sometimes used interchangeably, they refer to different scopes:
-
Arc Flash Analysis focuses strictly on energy calculations.
-
Analysis encompasses a comprehensive risk assessment, including system evaluation, personal protective equipment (PPE) requirements, label generation, and mitigation planning.
For more details on the technical side of energy modelling, see our dedicated Arc Flash Analysis page.
Such an analysis is a foundational safety process that protects lives and ensures your facility operates within the bounds of modern electrical safety standards. By identifying potential risks before they cause harm and implementing proper control measures, organizations can build safer workplaces and maintain operational integrity.
The Role of Electrical Hazard Studies in System Design and Maintenance
This type of analysis involves several integrated steps:
✔ System Data Collection
Documenting equipment specifications, one-line diagrams, protective device settings, and historical fault data.
✔ Short Circuit and Coordination Studies
Analyzing how faults propagate through the system and whether protective devices will operate safely.
✔ Arc Flash Calculations
Using IEEE 1584 equations to determine incident energy levels at critical points in the system.
✔ Boundary Determination and Labeling
Establishing safe approach distances and printing compliant arc flash labels for all relevant equipment.
✔ PPE Assessment
Identifying the required level of protection for each task based on calculated incident energy.
✔ Risk Assessment Documentation
Providing a written report that outlines all findings, assumptions, recommended safety procedures, and mitigation strategies.
Frequently Asked Questions
Who Should Conduct a Hazard Analysis?
Only qualified electrical engineers or safety professionals should perform a hazard analysis. These individuals must understand power system behavior, be familiar with applicable safety codes, and have experience using analysis tools. In many cases, third-party consultants are hired to provide impartial assessments and assist facilities in implementing corrective actions. A strong foundation in basic electrical safety is crucial when dealing with any energized equipment. The Basic Electrical Safety guide outlines essential practices to prevent accidents and ensure a safe working environment.
When Is It Required?
It is not a one-time task. It must be conducted:
-
At least every five years, per NFPA 70E and CSA Z462.
-
After system changes, including new equipment, reconfigurations, or setting adjustments.
-
Following any arc flash incident, it is essential to reassess risks and improve safety measures.
Keeping the analysis up to date is critical to maintaining accurate arc flash labels, valid PPE recommendations, and compliant documentation.
Benefits of Performing a Hazard Analysis
✔ Protects Workers from Injury or Death
Identifies risks before they cause harm, helping prevent burns, electric shock, and fatalities.
✔ Meets Legal and Regulatory Requirements
Demonstrates due diligence in complying with OSHA, NFPA 70E, and CSA Z462.
✔ Reduces Downtime and Liability
Minimizes the chance of electrical incidents that lead to costly repairs, investigations, or lawsuits.
✔ Promotes a Culture of Safety
Raises awareness among employees and fosters a proactive safety mindset in the workplace.
✔ Supports Insurance and Audit Readiness
Provides documented proof of hazard mitigation steps and employee training initiatives.
What does an arc flash hazard analysis include?
It includes a comprehensive evaluation of an electrical system to identify potential arc flash risks. It typically involves system data collection, short circuit and coordination studies, incident energy calculations, arc flash boundary determination, equipment labelling, and personal protective equipment (PPE) recommendations. The goal is to assess the severity and likelihood of arc flash events and implement measures to protect workers.
How often should hazard assessments be performed?
According to NFPA 70E and CSA Z462, arc flash hazard assessments should be performed at least once every five years. However, they must also be updated whenever significant changes occur in the electrical distribution system, such as equipment upgrades, system reconfigurations, or after an arc flash incident. Regular updates ensure that all labels, boundaries, and safety protocols remain accurate and compliant.
Is it required by OSHA?
While OSHA does not specifically use the term "arc flash hazard analysis," it does require employers to identify and protect workers from electrical hazards under the General Duty Clause and 29 CFR 1910 Subpart S. OSHA references NFPA 70E as a recognized standard for electrical safety. Therefore, conducting an analysis following NFPA 70E is considered a best practice for compliance and worker safety.
Related Articles:
On-Site Training
Interested in cost effective, professional on-site electrical training?
We can present an Electrical Training Course to your electrical engineering and maintenance staff, on your premises, tailored to your specific equipment and requirements. Click on the link below to request a Free quotation.
EF PARTNER MEDIA
Product Showcases
Shared Media