Arc Flash Analysis – Incident Energy and Boundary Calculations
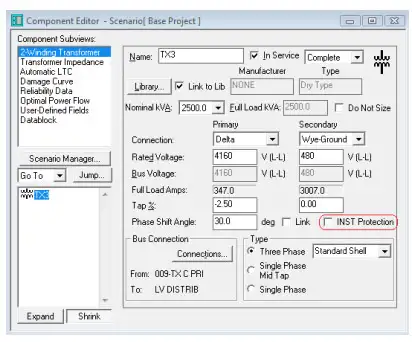
Arc flash analysis is a critical component of a comprehensive arc flash study — not a standalone procedure, but the phase where precise calculations determine the level of thermal energy that could be released during a fault. While the full arc flash study involves system-wide data collection and risk evaluation, arc flash analysis focuses narrowly on modelling specific hazards at individual points in the electrical system.
Request a Free Training Quotation
What Is Arc Flash Analysis?
It is the phase in which electrical engineers calculate the incident energy at key locations in a facility. This involves evaluating system parameters to identify the severity of a potential event and determining how far the resulting thermal energy could travel — known as the arc flash boundary.
This data is used to:
-
Specify the required PPE categories for safe work,
-
Mark electrical equipment with appropriate warning labels, and
-
Help organizations meet NFPA 70E and CSA Z462 compliance standards.
Unlike the broader study, which encompasses short-circuit analysis and coordination studies, the arc flash analysis itself focuses solely on the energy hazard associated with potential hazardous incidents.
Key Components
Arc flash analysis involves several technical steps that work together to assess the severity of potential uncontrolled incident energy events. Engineers begin by calculating available fault current at key points in the system, followed by precise calculations using IEEE 1584 formulas. These results are used to define appropriate PPE categories and boundaries. Specialized software tools streamline the process, ensuring accurate results and code-compliant documentation.
It is a critical process used to evaluate the potential for an explosion within an electrical system. By conducting a thorough arc flash risk assessment, safety professionals can identify the areas with the greatest hazards and determine the necessary steps to minimize them. This process involves a short circuit study to identify fault current levels and the behavior of protection devices under fault conditions. These devices play a vital role in limiting the release of energy during an electrical fault, helping to reduce injury and equipment damage. The analysis also accounts for working distance, which significantly affects the incident energy to which a worker may be exposed during a hazardous incident. It is essential to select the appropriate personal protective equipment (PPE) and establish safety boundaries.
Determining Available Fault Current
Engineers begin by calculating the maximum fault current at various points in the system, which directly affects the intensity of a potential explosion.
Calculating Incident Energy Levels
This is the heart of arc flash analysis. Using IEEE 1584 equations, the analysis determines the amount of energy (in cal/cm²) to which a worker could be exposed during a hazardous incident.
Defining PPE Categories
Once the energy levels are known, appropriate PPE categories (CAT 1 through CAT 4) are assigned to each piece of equipment, based on its hazard level.
Using Software Tools
Professional-grade software such as SKM PowerTools, ETAP, or EasyPower is commonly used to model system data, automate calculations, and generate detailed reports and one-line diagrams.
Use Cases for Arc Flash Analysis
The analysis is often employed in specific situations where a comprehensive study is not necessary. Common use cases include reviewing individual panels after equipment changes, verifying or updating warning labels, and performing spot checks to maintain compliance. It’s also used post-study to refine energy calculations or reassess hazard levels when system conditions change.
Targeted Equipment Reviews
Sometimes an arc flash analysis is performed on a single panel or circuit after changes are made or when labels need updating, without repeating the entire system study.
Spot Checks and Label Verifications
If maintenance or system updates occur, facilities may re-analyze only affected areas, ensuring ongoing compliance without a full study refresh.
Post-Study Refinements
Even after a study is complete, engineers may revisit the analysis portion to fine-tune results or respond to operational changes that affect energy levels.
Why Arc Flash Analysis Matters
It is essential for protecting workers and ensuring regulatory compliance. Accurately calculating incident energy levels and defining Personal Protective Equipment (PPE) requirements helps prevent serious injuries from electrical explosions. The analysis also supports the creation of accurate warning labels and helps companies meet safety standards like NFPA 70E and CSA Z462, making it a critical part of any electrical safety program.
By isolating and calculating the most dangerous points of potential incident energy, this analysis supports:
-
Worker safety by ensuring proper PPE is worn,
-
Label accuracy that informs workers of specific hazards, and
-
Regulatory compliance with OSHA, NFPA 70E, and CSA Z462.
It ensures that the energy levels associated with a hazardous incident are not just estimated, but precisely calculated, documented, and mitigated.
Arc flash analysis plays a crucial and focused role within the broader arc flash study. It provides organizations with the data they need to make safety actionable, from assigning the right PPE to establishing accurate protection boundaries. For a deeper understanding of the entire process, refer to our Arc Flash Study overview page.
Arc Flash Analysis vs Arc Flash Hazard Analysis
While arc flash analysis refers specifically to the technical calculations used to determine PPE requirements, it’s important not to confuse it with an arc flash hazard analysis. The hazard analysis is a broader risk assessment process that includes an analysis but also considers the likelihood of a hazardous incident. mitigation strategies, labeling, and compliance with safety standards like NFPA 70E or CSA Z462.
Related Articles:
On-Site Training
Interested in cost effective, professional on-site electrical training?
We can present an Electrical Training Course to your electrical engineering and maintenance staff, on your premises, tailored to your specific equipment and requirements. Click on the link below to request a Free quotation.
EF PARTNER MEDIA
Product Showcases
Shared Media